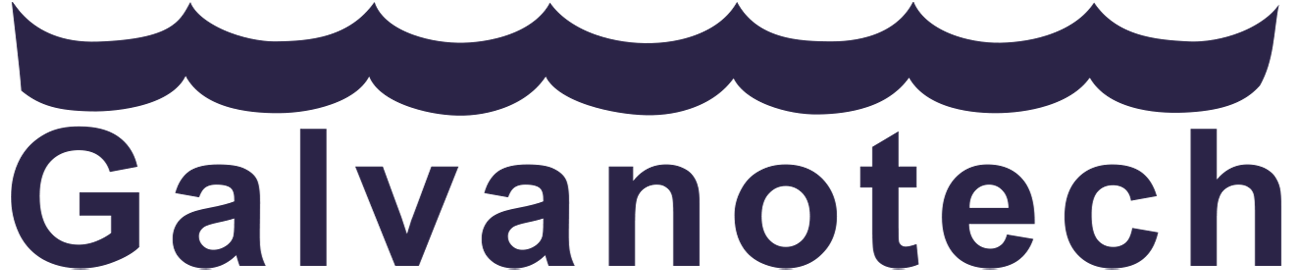
Our processes..
Mechanical Finishing
It is often required to remove burrs and sharp edges before commencing with any subsequent treatment, so as to improve the overall quality of the finished component.
On assessing the surface condition of incoming components, or on request by our customer, Galvanotech offer the following mechanical processes for improving the surface of your parts.
- Vapour blasting – This technique utilises a recirculating slurry of media in conjunction with adjustable air pressure to impart a fine finish on all metallic substrates. Although glass beads of various sizes are usually used, it is also possible to use abrasive media on challenging surfaces such as cast iron.
- Dry Blasting- This method of blasting uses adjustable air pressure to propel chosen media, whether abrasive or glass bead peening resulting in an adjustable blast profile or glass bead peenined effect.
- Vibratory polishing- Also known as vibro finishing, this method of deburring, and or polishing is an excellent way to prepare medium to large volumes of lighter parts for subsequent treatment. A very wide range of types and sizes of media are available, and in combination with the correct degreasing,deburring or polishing compound, various operations can be performed.
Masking
We pride ourselves on attention paid to detail in masking by hand using lacquers, tapes and other techniques to achieve excellent boundary definition.
Conversion Coating
Chromate conversion coating
Aluminium alloys readily oxidise in atmospheric conditions, making it necessary to treat the surface by converting surface aluminium into a compound which is corrosion resistant where bare aluminium is exposed, or as a base for subsequent painting or lacquering. We operate a proprietary, chromium free process which complies with the Mil-DTL-5541F, Type 2 Class 3 and 1A specifications as well as RoHS directive.
Sulphuric acid anodising
Anodising of aluminium alloys imparts a tough protective layer over exposed surfaces which can be dyed a multitude of different colours or left in its natural state. We specialise in smaller components which require special attention or customer requirement such as precision machined housings etc. Our process meets the requirements of Mil-A-8625, Type 2, Class 1 and 2.
Hot Blackening
Hot blackening imparts a rich black conversion coating to ferrous materials, as well as most stainless-steel alloys. It serves a cosmetic function, and also acts as a temporary corrosion barrier, which can be enhanced by using an appropriate oil topcoat.
Zinc Phosphate
A process mainly for ferrous materials, which is typically used as a key for adhesion of polymer topcoats. The microcrystalline layers produced during the process significantly increase the surface area for adhesion, or absorption of lubricant. Our process meets the requirement of DEFSTAN 03-11/1, Class II.
Electroless Nickel
Deposits produced from these processes offer great flexibility in deposit properties such as hardness, wear resistance, corrosion resistance, solderability, lubricity or optical performance. Coating properties can be tailored to customer requirement by selecting the correct EN process for the application.
We are able to apply a wide range of electroless nickel with phosphorous contents varying from 2-11% phosphorous on substrates that include steel, stainless steels, all grades of aluminium, titanium and also some non-conductive surfaces. Layer thicknesses are tightly controlled and thicknesses of 5- 200 microns are possible. Composite EN PTFE coatings are also possible, which greatly reduce friction.
The most common specifications adhered to are ISO-4527, AMS-2404 and ASTM-B733.
Polymer Coatings
At Galvanotech we are applicators of various polymer topcoat systems that overcome a number problems such as corrosion resistance,mitigating hydrogen embrittlement, lubricity, stray light suppression, EMI shielding, and of course cosmetic purposes.